Step one
Find the most suitable inspection machine for your product
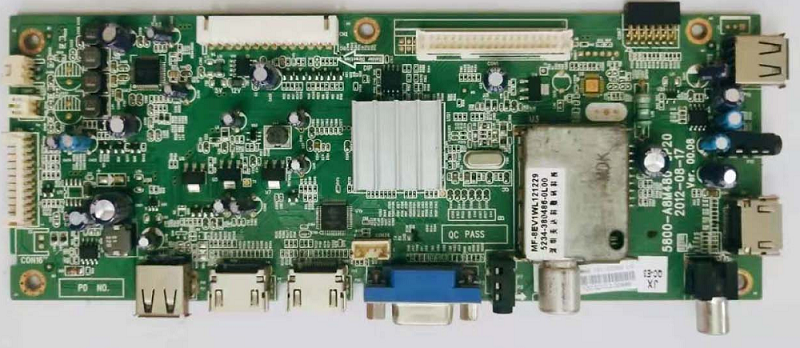
PCB inspection
X-RAY inspection machine is widely used in PCB, BGA chip inspection, LED, SMT, semiconductor, electronic product inspection, iron and aluminum die castings, electrical and mechanical parts, automation components, and other industries. However, the inspection requirements of each industry or product are different, so, there are many different types of X-ray inspection machine, users still need to be clear about their needs and find the most suitable inspection machine.
For example, if you are a PCB substrates manufacturer, you need to check whether the through holes reserved for each layer of the substrate are aligned, you need to use a multilayer PCB X-ray inspection machine.
If you are a manufacturer of LED lights and SMT PCBA, you need to detect the PCB soldering quality, such as BGA solder balls, QFP, QFN chips, etc., you need to use micro-focus X-ray inspection machine.
If you are a car manufacturer, you need to detect the hub or aluminum alloy cylinder block of your engine, etc., you will need the non-destructive testing X-ray inspection machine.
There are many types of testing machines for different applications. If you have any questions, you can call us by +8618406666351, or send an email to [email protected].
Step two
Determine how many kilovolts and how accurate the X-ray tube you need.
Different products have different material density, thickness, and detection accuracy. For example, the ordinary civilian PCB requires an X-ray tube of 90KV and about 5 microns. For a thicker military PCB, the thickness may exceed 3 mm, 5 mm, it needs X-rays above 130KV. Source. Micro-focus X-ray source brands are also important, currently, there are mainly two brands, Hamamatsu in Japan and Thermo Fisher in the United States. The life span of Hamamatsu in Japan is relatively long, but the price is slightly expensive. Wellman X-ray inspection machine can be equipped with Hamamatsu 90-130KV X-ray tubes, with long life and maintenance-free.
Step three
Decide whether you want a flat panel detector or an image intensifier, what size do you need?
The X-ray receiving device can capture the X-ray passing through the object and convert it into an image presented in front of the user’s eyes. Users can see BGA welding defects and cracks in castings in X-ray images.
Flat-panel detectors have the characteristics of small size, high definition, and high brightness compared to image intensifiers, but the disadvantage is that they are expensive.
Some users’ products are relatively large, such as the server PCB. Sometimes it is necessary to quickly detect the overall BGA with a length of 5 cm. It may be necessary to use a large-area flat-panel detector. Image intensifiers that are generally about 4 inches in size are almost stretched.
Step four
Machine structure
The structure determines the inspection range, function, and convenience of the X-ray inspection machine. Advanced X-ray inspection machine may have a 60-degree tilt observation, the table can rotate 360 degrees, color image navigation, 3D CT tomography, and other functions.
Wellman X-ray inspection machine uses a flat-panel detector tilt structure. Compared with the old-fashioned machine that uses image intensifiers from some manufacturers, it has a huge performance advantage. For details, see our article: http://www.wmxray.cn/NewsDetail/1517879.html
Step five
Software function
Manufacturers with independent software intellectual property rights are the premise to ensure the legal use of your machine software. Perfect software functions can bring you more convenience.
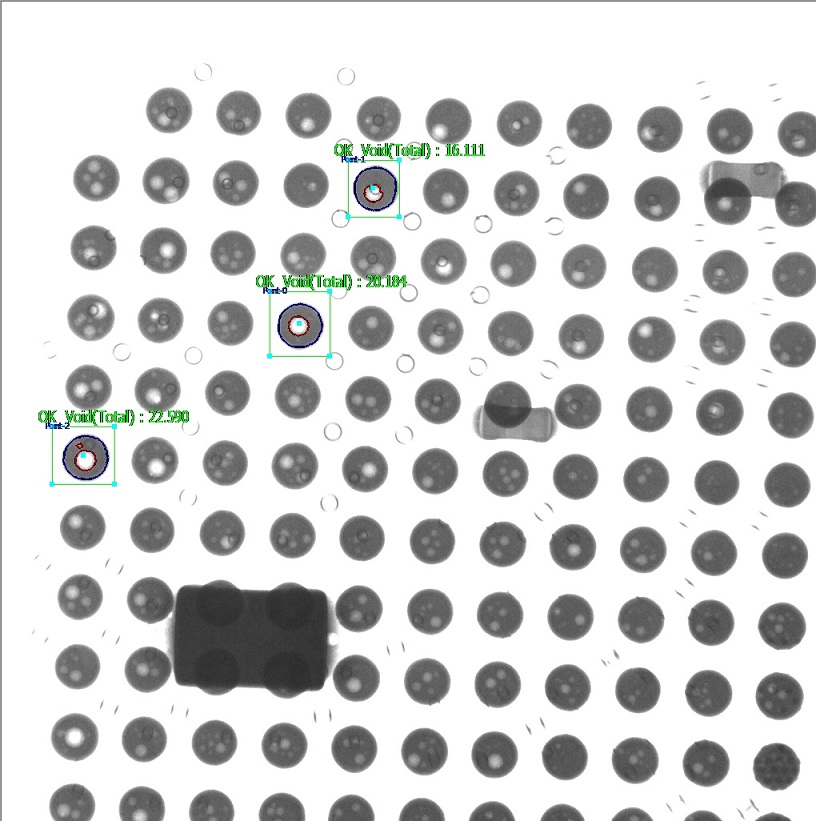
PCB BGA X-ray inspection
Step six
After-sales service
Wellman X-ray inspection machine provides you with the longest warranty period in the industry and better after-sales service. It is the best choice for you to purchase equipment without any worry!
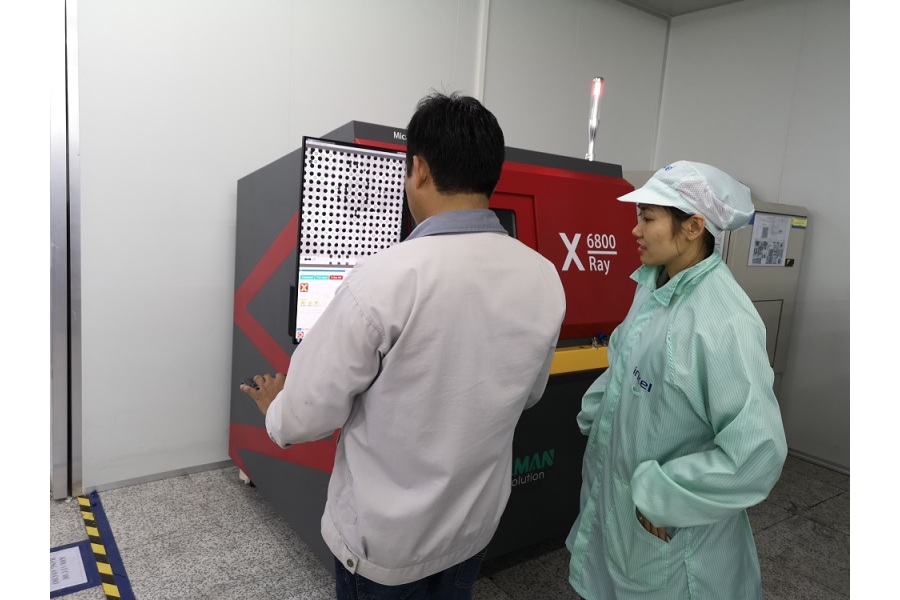
Wellman after-sales service